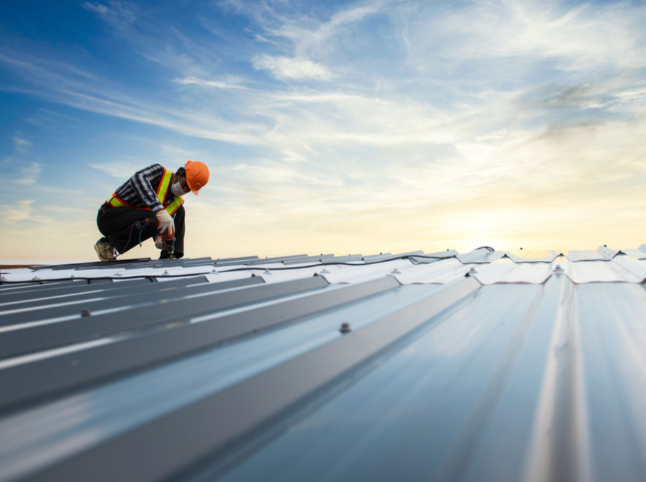
In the realm of modern manufacturing, structural durability, scalability, and efficiency are non-negotiable. Whether you're establishing a new production facility or expanding an existing plant, the decision of who builds the structure can make a significant impact on long-term operations. For many manufacturers, partnering with industrial steel building contractors offers the ideal solution.
Steel buildings have become synonymous with industrial development for good reason—they offer design flexibility, cost efficiency, and long-lasting performance. Choosing contractors who specialize in steel construction ensures that these benefits are fully realized while aligning with the functional demands of manufacturing spaces.
Why Steel Buildings Suit Manufacturing Needs
The physical and operational demands of a manufacturing unit—whether for assembly lines, storage, or heavy machinery—require buildings that are:
Structurally strong and secure
Adaptable to changing layouts and workflow
Resistant to wear, corrosion, and environmental elements
Easy to maintain over time
Industrial steel construction in Oregon and across the U.S. has evolved to meet these exact requirements. Compared to traditional building materials, steel provides superior load-bearing capabilities and longevity, making it ideal for facilities that demand performance under high-stress conditions.
How Industrial Steel Building Contractors Add Value
1. Specialized Expertise in Design and Engineering
Industrial steel building contractors offer more than basic construction skills—they bring targeted knowledge of steel-specific structural engineering. Their teams are trained to design buildings with wide, column-free interiors that optimize production flow and storage use.
They also handle the unique needs of manufacturing units, including:
Crane-support systems
Mezzanine levels for vertical storage
Insulated panels for energy efficiency
Custom bay spacing to accommodate large machinery
This level of customization is key to supporting the operational efficiency of a manufacturing plant from day one.
2. Efficient and Scalable Construction Process
Time is a critical factor in manufacturing, where delays in facility readiness can result in production losses. Steel building contractors are known for their ability to expedite project timelines through:
Pre-engineered steel components
Streamlined assembly techniques
Experienced metal building erectors who can mobilize quickly
In Oregon and other regions with seasonal weather challenges, rapid construction means reduced weather-related downtime and earlier occupancy.
3. Durability and Long-Term Cost Control
Steel buildings are designed to endure decades of use with minimal structural degradation. This resilience translates to fewer repairs and lower insurance premiums. Unlike wood or masonry, steel resists:
Termites and other pests
Mold and mildew
Fire and extreme weather
By using steel as the primary material, manufacturers reduce long-term maintenance liabilities—especially when supported by proactive metal building maintenance routines handled by the same contractors who built the structure.
4. Compliance with Industrial and Environmental Regulations
Industrial zones often have strict regulations for structural integrity, fire safety, air quality, and energy efficiency. Reputable steel building contractors are well-versed in local, state, and federal compliance requirements.
In regions like Oregon, where environmental standards can be rigorous, these contractors help ensure:
Proper stormwater management
Eco-friendly insulation choices
Efficient lighting and ventilation integration
This built-in regulatory awareness helps prevent costly delays or post-construction adjustments.
5. Seamless Maintenance and Repair Services
A major benefit of working with dedicated industrial steel building contractors is the continuity of service. Many contractors offer metal building maintenance packages, which may include:
Annual structural inspections
Roof and panel assessments
Sealant and joint upkeep
Fastener tightening or replacement
This ensures the building continues to perform well long after construction is complete. Maintenance programs tailored to manufacturing units help minimize production downtime due to building-related issues.
Why Oregon Businesses Rely on Metal Building Erectors
Oregon’s industrial sectors—from food processing and metal fabrication to renewable energy and equipment manufacturing—depend heavily on robust, adaptable infrastructure. Local metal building erectors understand the regional climate, permitting processes, and logistical demands that come with industrial-scale projects.
Choosing contractors experienced in industrial steel construction in Oregon offers peace of mind, knowing the project will adhere to structural codes, environmental regulations, and performance expectations suited to local industries.
Final Thoughts
For manufacturing businesses aiming to build or expand a facility that is strong, adaptable, and cost-effective, working with industrial steel building contractors is a strategic decision. Their specialized knowledge, streamlined construction processes, and continued support through metal building maintenance make them well-equipped to meet the demands of a dynamic industrial environment.
By partnering with professionals who understand both the material and the mission, manufacturers set the foundation for long-term operational success—literally and structurally.
Write a comment ...